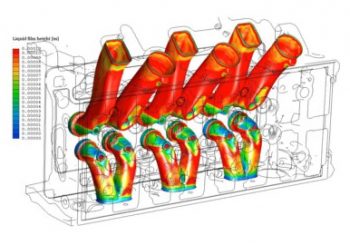
A 2013-ban végrehajtott szimuláció, amely a forgács lefúvató berendezés üzemeltetőjének azóta minden másodpercben hasznot termel, 2014-ben újabb kihívásokkal folytatódott. A DELTA-TECH Kft. győri irodájának projektvezetésével zajló fejlesztés újabb szakaszában tovább javítottuk a szimulációval optimalizált tisztítási teljesítményt. De vajon egy sikeresen lezárt hengerfej tisztítás CFD szimuláció folytatásában milyen újabb kihívások jöhetnek még?
A 2013-as projekt arról szólt, hogy egy osztrák cég által gyártott, sűrített levegővel működő tisztítócella levegőfelhasználását csökkentsük. Ezt akkor úgy oldottuk meg, hogy a teljesen felesleges mozgásokat megszüntettük, a levegőhasználat idejét pedig a szükséges minimumra korlátoztuk, mindezt CFD szimulációkkal előkészítve. És ezek a mozgások bizonyítottan feleslegesek voltak, mert a gép köszöni szépen teljesen jól végzi a dolgát ezek nélkül is. Ez minden öntvény tisztítása után bizonyítást nyer azáltal, hogy ha a tisztítás után végzett mérés zavarmentesen lezajlik, akkor a sűrített levegős lefúvatás is rendben van. A 2013-as szimulációkról készült cikk itt olvasható, abban írtam a forgácsok modellezéséről és a lefúvatási idő meghatározásának módszeréről is.
2014-ben eggyel magasabbra került a léc.
Tovább kell csökkenteni a felhasznált energiát
A már korábban optimalizált levegős lefúvatást kellett tovább javítani, még hatékonyabbá, még kisebb energiaigényűvé tenni. Az öntvény – egy 3.0L V6 diesel egyik hengerfeje – ugyanaz, hogy össze lehessen hasonlítani a korábbi vizsgálatokkal, ugyanazokat a forgácsokat használtuk és velük kapcsolatos paraméterek is azonosak a korábbi szimulációval, de minden másnak mennie kellett.
A cél 2014-ben tehát az volt, hogy a tisztítás összesített energiaigényét csökkentsük. Tegyük fel a példa kedvéért, hogy a 2013-as vizsgálatok előtt egy hengerfej tisztításához ebben a bizonyos lefúvató berendezésben 12kW energiára volt szükség. Az első szimuláció után ez mondjuk 10kW-ra csökkent és a vizsgált gép így jól is üzemelt. Mit lehet ezen még javítani?
Az új technológia a Delta-Tech győri szakembereinek ötletén alapult, amely az öntvényre nem fújja a levegőt, hogy a forgácsok szerte-széjjel repüljenek, hanem több, speciálisan ehhez az öntvényhez tervezett elszívó fejjel és egy megfelelően méretezett ipari porszívóval elszívja azokat.
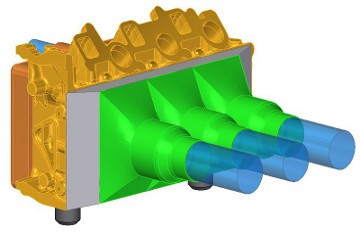
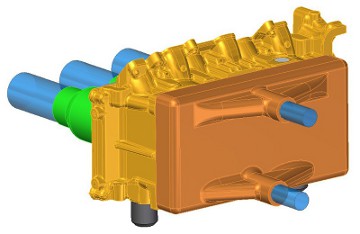
A koncepció megalkotása CFD szimulációval
A CFD szimulációkkal pedig az volt a feladatom, hogy a koncepcionális modellből kiindulva mondjam meg, hogyan nézzen ki a széria elszívófej, mennyi ideig kell a fejet az öntvényen tartani ahhoz, hogy a forgácsokat teljesen el tudjuk távolítani.

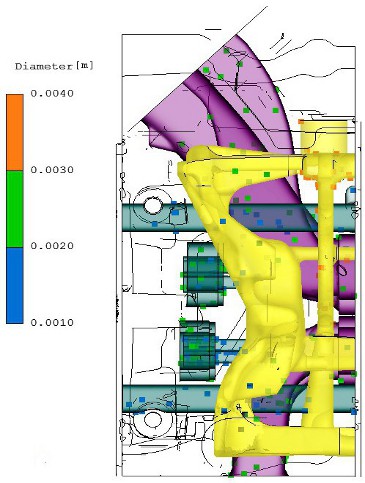
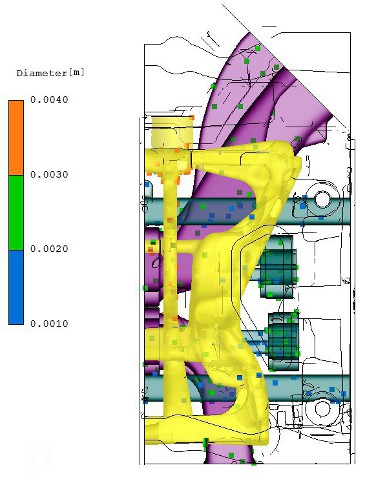
Továbbá az elszívófejeknek az öntvényen keresztül mikor és mennyi levegőt kell mozgatniuk ahhoz, hogy a tisztítási teljesítmény jobb legyen, mint volt. Vagy olyan alapvető kérdésekre válaszolni, hogy az öntvénynek melyik nyílásához kell elszívó fejeket tenni és melyeket kell szabadon hagyni, és a többi.
Sok verzió van és a szimuláció sokáig tart
Röviden összefoglalva: állandóan változó modellekkel kellett szimulációkat készíteni. A dolog további szépsége, hogy a modellekre épített hálók elemszáma 9 és 11 millió között mozgott (az sok). És mivel időben változó folyamatokat modelleztünk, akár 15 másodperces elszívási idő vizsgálatára is szükség volt.
Ez elsőre nem tűnik olyan borzasztóan bonyolultnak, mert 15 másodpercig gyalogolni igazán nem nagy kunszt. De mi van akkor, ha egy lépés csak a másodperc ezred részéig tarthat? Szimulációs paraméterekre lefordítva ez azt jelenti, hogy a 15 másodpercet 0.001 másodperces időlépésenként kellett kiszámolni. Ez azért ilyen kicsi, mert a szimulációk stabilitását ilyen érték biztosította a modellezett térben megjelenő sebesség állapot mellett. Ebből adódik, hogy 15000 iterációt kellett végrehajtani egy 10 millió elemes hálóval. Sokáig tart, na. És sokszor kellett ugyanezt eljátszani, mivel már fejlesztünk, nem csak egy kész dolgot modellezünk.
Tehát már az elején látszott, hogy itt rengeteget kell majd számolni. Így az SC/Tetrával találnom kellett egy olyan módszert, ami lehetővé teszi, hogy a szimulációk eredményeinek elemezése utáni geometria változtatásokat gyorsan be tudjam építeni a modellbe és a lehető legrövidebb időn belül újra indulhasson a futtatás.
Modulokból épített háló az előkészítési idő csökkentésére
Ismerős az autóiparban jelenleg használatos moduláris platform rendszer?
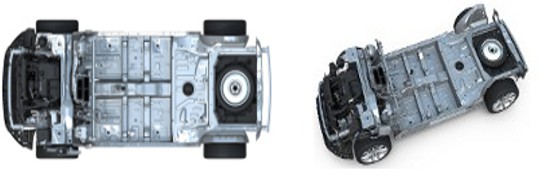
Forrás: www.psa-peugeot-citroen.com
Ez a platform rendszer annyit jelent, hogy a jármű alapját egy főegységekből (például a kocsi eleje motorral és futóművel, a kocsi közepe az utascellával, a kocsi hátulja a futóművel) összeállítható váz alkotja, amire különböző alakú karosszériákat tervezhetnek. Így épül ugyanarra a vázra háromajtós, négyajtós, kombi vagy SUV.
Mivel minden más módszer borzasztóan időigényes lett volna, én is ezt választottam. Csak nálam a modulok az öntvény egyes oldalaihoz csatlakozó elszívó fejek voltak. A központ a hengerfej és a közvetlenül körülötte lévő levegő térfogat, amelynek minden lényegesebb oldalára – ahová egyáltalán elszívók csatlakoztatása elméletileg lehetséges volt – az SC/Tetrában olyan feltételeket írtam elő, amelyeken nem volt szükség a csomópontok pontos illeszkedésére. Ezt a funkciót mi csak úgy hívjuk: nem folytonos háló (discontinuous mesh).
Csak a megváltozott háló modulokat kell cserélni
Így aztán teljesen mindegy volt, hogy a központi 6.6 millós elemszámú öntvényhez mit csatlakoztatok és annak milyen méretű elemekből épült a hálója. Bár alapvetően úgy intéztem, hogy a csatlakozó felületek mellett az elemek mérete azonos legyen. Ettől távolabb lehetett nagyobb és kisebb is, ahogy a modul geometriája megkívánta. Ha az egyik oldalon le akartam cserélni az egyik elszívófejet, a csatlakozó felület helyzetét megtartva kicseréltem a hálót az új verzióéra és már indítottam is a következő szimulációt.
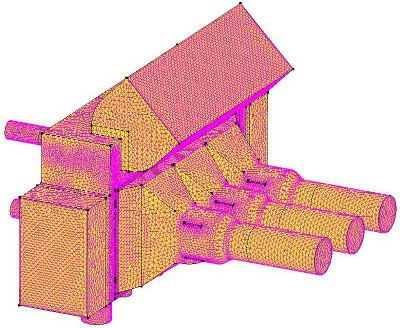
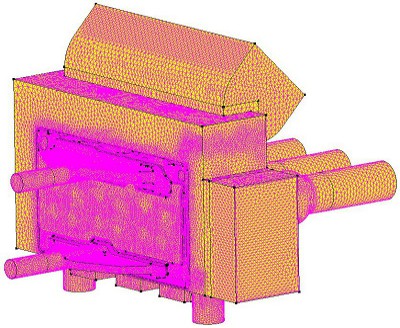
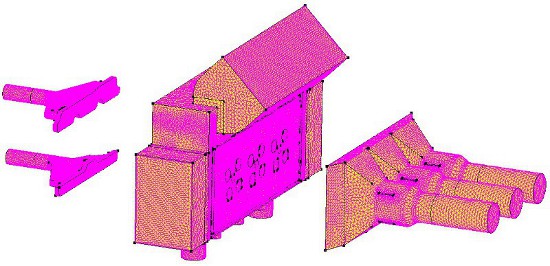
Ha pedig van egy működőképes módszer arra, hogy több verziót próbáljunk ki áramlástani szimuláció segítségével, akkor ezeket összehasonlítva egymással és a 2013-as vizsgálat eredményeivel következtethetünk arra, hogy az éppen kiszámított elszívócsonk változat milyen tisztítási teljesítményt produkálna majd a valóságban.
A cikk következő részében írok az összehasonlítás eredményeiről és egy új SC/Tetra funkcióról, amit az elszívás alatt az öntvény felületein lévő emulzió réteg vastagságváltozásának szimulációjára használtunk.
Dr. Dúl Róbert