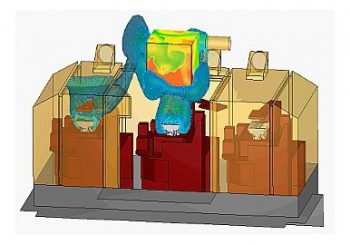
A levegőbe kerülő szennyezőanyagok terjedésének áramlás- és hőtani szimulációs vizsgálatáról már jelent meg egy esettanulmányunk, ahol egy vegyipari üzem légterébe került szén-dioxid terjedését vizsgáltuk. A CO2 kibocsátás a technológia része volt és 50m-rel a talajszint felett történt, de az ipari berendezések üzemeltetése során előfordul, hogy a nemkívánatos anyagok a gépeket kezelő személyzethez sokkal közelebb szabadulnak fel. Ez a cikk egy két részből álló füst elszívás CFD szimuláció esettanulmány első része.
Az ártalmas anyagok kibocsátásához tartozik a legkülönbözőbb módon keletkező por és füst levegőben való terjedése, de szóba kerülhet a laboratóriumok berendezéseiből ártalmas gázok szivárgása is. Különösen fontos e folyamatok számítógépes modellezése akkor, ha zárt térben nagy mennyiségű légszennyező keletkezik, például ha egy évente 3 millió hengerfejet előállító öntöde egyik gyártócsarnokáról van szó.
Öntvények nagy motorokhoz
Audi S8, R8, S6, RS6, Lamborghini Gallardo, Huracán. Vajon mi a közös ezekben az autó típusokban? Az, hogy ezekbe szerelték a VW V10-es benzinmotorjának különböző változatait, és hogy elég nagy a valószínűsége annak, hogy a hengerfejek Közép-Európa egyik legnagyobb öntödéjében, Magyarországon készültek. A 3 millióból persze nem mind V10-es motorhoz való, a legtöbb hengerfej 1.5 vagy 1.6 literes diesel, illetve 1.4, 1.6 vagy 2 literes turbós benzinmotorba kerül.
Legyen azonban bármilyen méretű a hengerfej, egy biztos. Ha egy öntöde azt a technológiát használja, mint a mostani esettanulmányban szereplő, akkor az öntés folyamata során változó, bizonyos esetekben jelentős mennyiségű füst keletkezésére kell számítania.
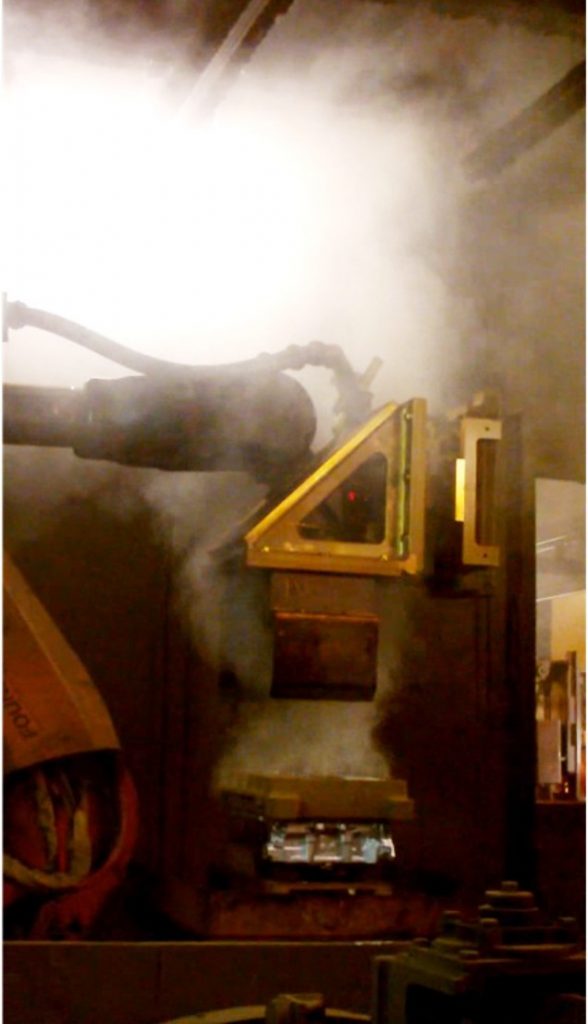
De mi is ez a füst egyáltalán? Honnan szabadul fel? Mikor és főleg mennyi?
A szerves gyanta égése miatt füstölnek a magok
Nos, ez a füst az öntvény üregeit képező homokmagokból szabadul fel a homokszemcséket összetartó gyanta elégése miatt, és kis mennyiségben rögtön megjelenik, amint a 700°C-os alumínium olvadékot elkezdik beönteni a formába.
Ahogy az alumínium hőmérséklete csökken, úgy forrósodik át az összes belső homokmag és így keletkezik egyre több füst is. A levegőbe jutó mennyiség pedig hirtelen a sokszorosára nő akkor, amikor az öntőszerszám kinyílik, és a füst az addig a kokillába zárt homokmagok külső felületein keresztül is szabadon távozhat.
A füstképződés tehát itt is a technológia része, ami viszont a kihívást jelentette az öntöde számára az, hogy az üzem a technológia fejlesztése miatt sokkal több és nagyobb tömegű öntvényt (és így több füstöt) állított elő, mint amire az öntőgépek burkolatát 10 éve tervezték. Az elszívási technológiát fel kellett fejleszteni arra a szintre, amely képes kezelni még a jelenleginél is nagyobb öntvény darabszámot.
Csakhogy az elszívott füstös levegőt ártalmatlanító berendezés kapacitása véges és nem terveztek millió eurókat egy új légkezelő beüzemelésébe borítani. Tehát a meglévő kapacitást kellett újraosztani, hatékonyabban felhasználni. Ide kellett az áramlástani szimuláció!
Az elszívott légmennyiség optimalizálása
Mi azt a testhezálló feladatot kaptuk, hogy CFD szimuláció felhasználásával tervezzük át az öntőgépek burkolatát úgy, hogy – optimális esetben – ne szabaduljon ki füst a burkolat alól. Ezt úgy kellett elérnünk, hogy az elszívási kapacitást gépenként 8500 m3/h-ra limitálták, 60°C-os levegő hőmérsékleten.
Egy ilyen kaliberű fejlesztési feladat esetén a legelső lépés az, hogy rögzítjük a kiindulási állapotokat. Ezt az állapotot szimulációval elő is állítjuk. Így lesz egy, a valóságot jól leíró peremfeltétel rendszerünk és kiindulási öntőgép geometriánk. Erre alapozva majd értékelni lehet, hogy a módosított változatok jobban teljesítenek-e.
Kiválasztottuk tehát azt az öntőgépet, amely a legnagyobb tömegű hengerfejet gyártja. Elkészítettük a térbeli számítógépes modelljét, valamint videóra vettünk több öntési ciklust is. Az alábbi kép az öntőgépet elölről mutatja és a méreteit jól érzékelteti az operátor fekete színű modellje.
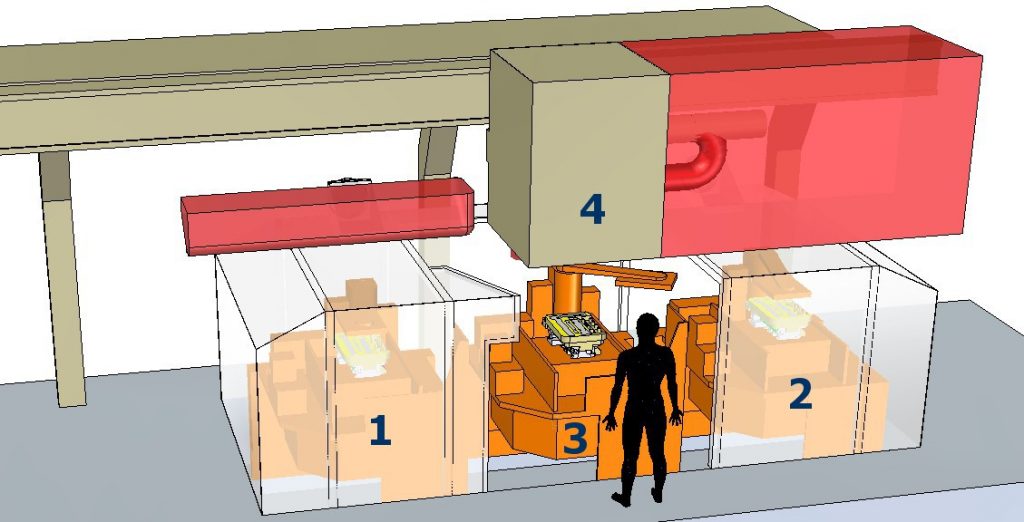
Az acél lemezből készült burkolatot a képen áttetszővé tettük, hogy látható legyen a burkolat alatt elhelyezkedő két, narancs színű kokilla is az öntvényekkel. A számítógépes modellben négy olyan fontos pozíciót helyeztünk el (a fenti képen számokkal jelölve), ahol a videó felvételek tanúsága szerint az öntvény füstöt bocsát ki. A négyből három az operátor magasságában, a negyedik pedig az ábrán nagy barna dobozként megjelenő, elszívással is ellátott manipulátor belsejében, a talajszinttől 2m magasságban volt.
A képen pirossal olyan tereket jelöltünk, amelyben segédberendezések mozogtak. Ezeket mindenképpen szabadon kellett hagynunk az átalakítások megtervezése során. Bal oldalon az automatizált öntőkanál, jobb oldalon pedig a manipulátor, amely a kokillából veszi ki a friss és füstölő öntvényt és viszi a következő munkahelyre.
Az öntőgép hátulján – amelyet a következő ábra mutat be – találhatók a burkolat felső részén kialakított, meglehetősen kis méretű elszívóernyőkhöz csatlakozó, kék színű elszívócsövek, a kiindulási állapotban 3db van belőlük. A vörös színnel jelölt, a többinél kisebb átmérőjű flexibilis cső a manipulátor burkolat elszívását végzi.
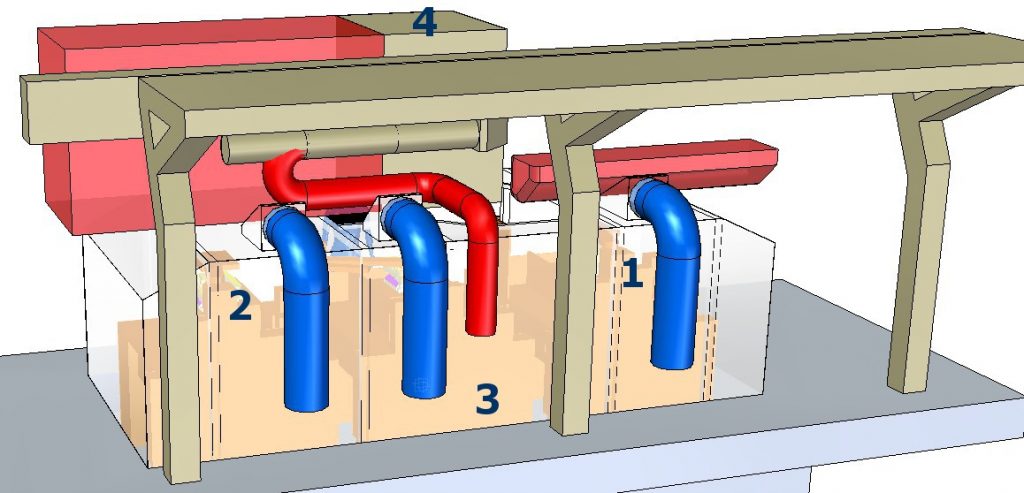
Videókon rögzítettük azt, hogy az öntési ciklus alatt hol, és milyen intenzitású füst képződik. Rögzítettük, hogy hol szabadul ki a burkolat alól és főleg, hogy a cikluson belül meddig tart a normál és meddig a nagy intenzitású, kokillanyitás utáni füstölés.
A képeken számozott négy pozíció egy egyszerűsítés eredménye, ugyanis az öntőgépben csak két öntvény, tehát két kokilla van. Ezek viszont vízszintesen mozognak a burkolat alatt és váltják egymást az operátor előtti, felülről nyitott térben. A négy számozott pozíció megfelel azoknak a helyeknek, amelyeket a két öntvény az öntési ciklus alatt bejár. De a valósággal ellentétben a szimulációban nem a füstölő önvényt mozgattuk (lehetséges, de bonyolult és sokkal lassabb, mint ez a módszer), hanem a füst keletkezésének helyét változtattuk úgy, hogy szinkronban legyen az öntvények valós mozgásával.
A gép nem mozog, csak a füst keletkezési helye
Az alábbi képek az öntési ciklus jellegzetes állomásait mutatják be. A füstöt a kék színű felület szemlélteti.
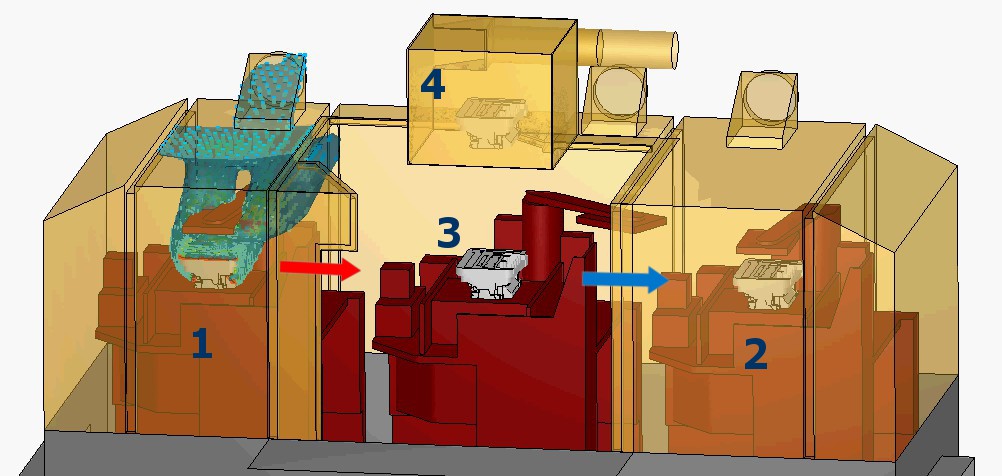
1. pozícióban öntvény szilárdul és normál intenzitással füstöl; 2. pozíció üres; 3. pozícióba az operátor homokmagot rak; 4. pozíció üres
A fenti képen látható piros nyíl azt mutatja, hogy a ciklus következő lépésében az 1. pozícióban lévő füstölő öntvény a 3. pozícióba mozog majd. Miután a 3. pozícióban lévő kokillát feltöltik alumíniummal, az a 2. pozícióba mozog majd és ott kezd el füstölni. Ezt mutatja a kék nyíl.
A ciklus 2. lépésében az elszívórendszernek már két helyen kell füstöt kezelnie, ahogy azt az alábbi ábra is mutatja.
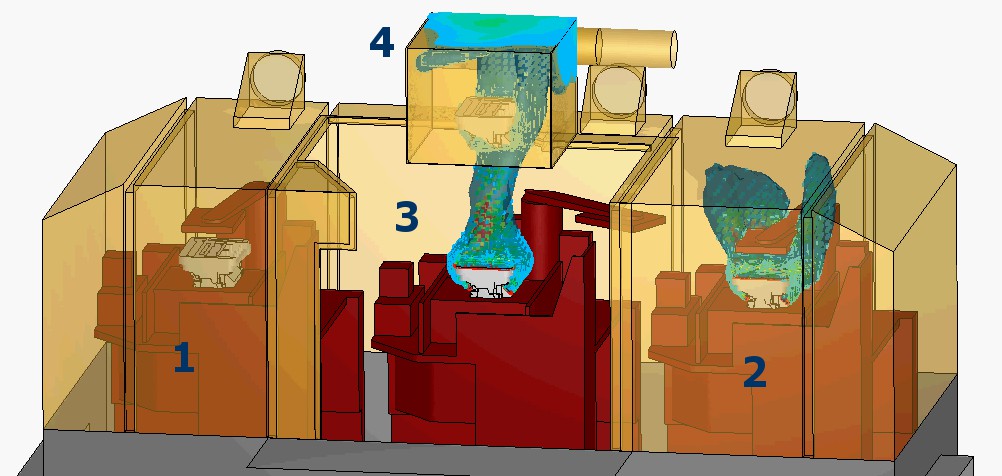
1. pozíció üres; 2. pozícióban öntvény szilárdul és normál intenzitással füstöl; 3. pozícióban öntvény szilárdul és normál intenzitással füstöl, kokillanyitásra vár; 4. pozíció üres
A megszilárdulás elején tartó öntvény a 2. pozícióban normál intenzitással füstöl a burkolat alatt. Az 1-esből a 3. pozícióba mozdult öntvény viszont már jól átforrósította a homokmagokat. Egyre több füst száll fel belőle, és a kokilla nyitására vár. Ez a következő lépésben meg is történik az alábbi ábra szerint.
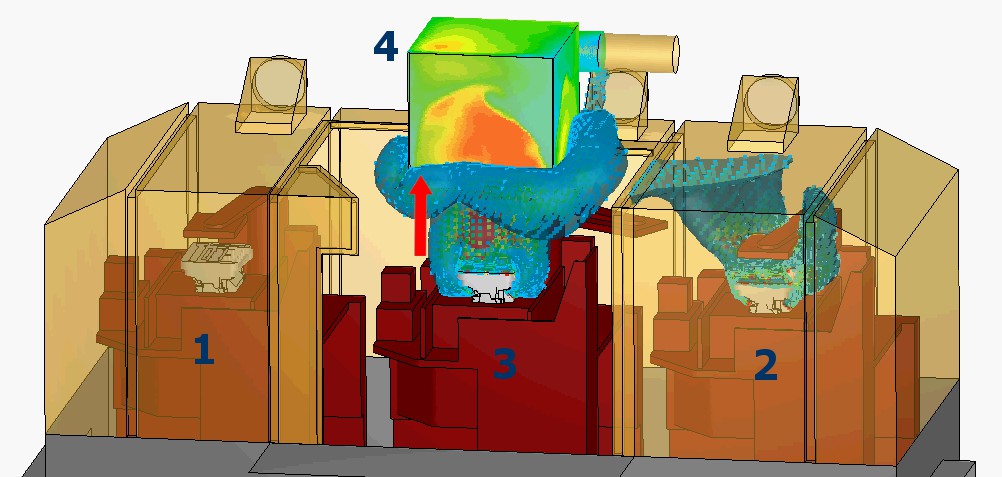
1. pozíció üres; 2. pozícióban öntvény szilárdul és normál intenzitással füstöl; 3. pozícióban kokilla nyit és az öntvény nagy intenzitással füstöl; 4. pozíció üres
A kokilla nyitásakor felszabaduló füst hirtelen és a normál állapothoz képes 3-szoros intenzitással jelenik meg a 3. pozícióban. Ezt a valóságban és a szimulációban sem képes kezelni a 4. pozícióban lévő, doboz alakú elszívóernyő. A fenti ábrán látszik is, ahogy a kék füstfelhő az elszívódoboz szélei mellett a csarnok léterébe távozik.
A 3. pozícióból az intenzíven füstölő öntvényt az ábrán látható piros nyílnak megfelelően a manipulátor kiemeli a kokillából (az elszívódoboz nem mozog vele) a 4. pozícióba. Majd a füstölés itt megszűnik, mert a valóságban a manipulátor az elszívódobozban lévő öntvénnyel együtt elmozog jobbra, ahol is azt a következő munkahelyre teszi le. Ekkor az öntőgépben minden kezdődik előröl. Most a 2. pozícióban van normál intenzitással füstölő öntvény, miközben a 3. pozíció üres kokillájába az operátor berakja a magokat.
A következő ábrán a piros nyíl azt mutatja, hogy a ciklus következő lépésében a 2. pozícióban megszilárdulás alatt lévő, normál intenzitással füstölő öntvény a 3. pozícióba mozdul. A 3. pozícióban a magokkal felöltött kokilla a fém beöntése után az 1. pozícióba kerül és normál intenzitással füstölni kezd.
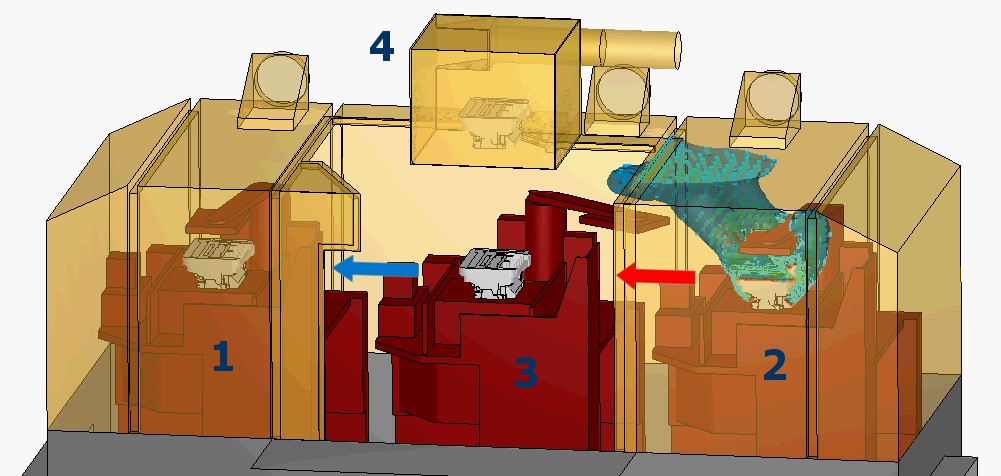
1. pozíció üres; 2. pozícióban öntvény szilárdul és normál intenzitással füstöl; 3. pozícióba az operátor homokmagot rak; 4. pozíció üres
A teljes füstölési folyamat tehát így néz ki:
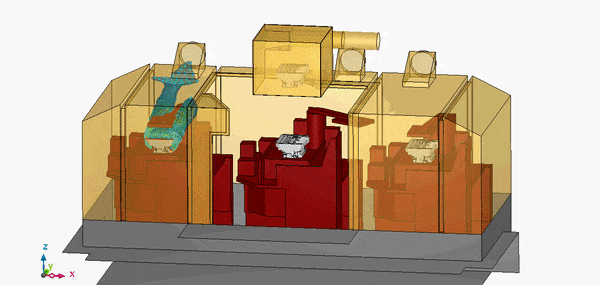
Mindaz a füst, amelyet a hátfalhoz közel a burkolat tetején kialakított, ék alakú elszívóernyőkhöz illesztett csövek nem tudnak összegyűjteni és eltávolítani, bizony kilép a burkolat alól és a csarnok légterébe távozik.
Ez több szempontból is kellemetlen. Egyrészt a burkolat alatt, az 1. és 2. pozícióban lévő öntvényből felszabaduló füst pont a 3. pozícióban a magokat rakodó operátor fejmagasságában lép ki a burkolat alól. Másrészt az itt lévő összes öntőgép által kibocsátott füst elég gyorsan képes beteríteni a teljes csarnokot. Tehát a füstöt minden eszközzel a burkolat alatt kell tartani. Az öntőgép helyi elszívását kell úgy kialakítani, hogy az elszívórendszer képes legyen az évek alatt jelentősen megnőtt öntvény darabszámmal járó füstkibocsátást is kezelni.
Hogy ezt hogyan valósítottuk meg, a cikk következő részéből kiderül. Az esettanulmány 2. részét itt olvashatod.